以高效且可持续的方式保护零件免于生锈。
(ECOCLEAN GROUP 销售总监/产品线经理 RAINER STRAUB)
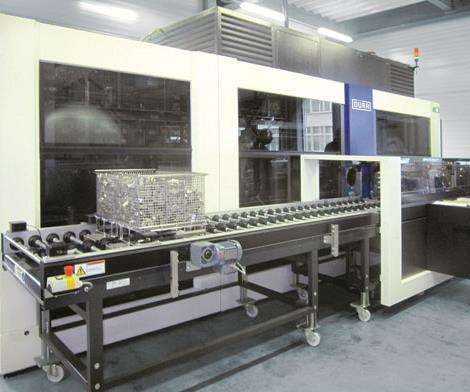
真空吸尘
现代的全封闭真空清洁系统可在一台机器中实现高效、安全的清洁和防锈保护——甚至是长期的。加工后零件将 100% 干燥。
在制造期间和之后,工业零件清洁的任务是满足进一步加工或工件组装所需的表面清洁度规范。根据污染情况,非卤代烃和改性醇表现出明显的优势。它们不仅确保可靠、高效和可持续地去除油、冷却剂和切屑,而且还允许在一台机器上执行清洁和腐蚀保护过程——甚至是长期保护。
金属零件在制造和加工操作过程中不可避免地会变脏。冷却液残留物以及切屑和颗粒等异物通常会成为热处理、焊接、涂层或组装等下游加工过程中的问题。此外,污染物可能会损害成品的质量、功能和使用寿命。
因此,工业零件清洗是生产链中不可或缺的一步。最常用的技术是湿化学清洗。
“同类相溶”原则
清洁过程的效率以及质量、成本效率和稳定性在很大程度上取决于所用清洁剂的溶解能力。水性清洁剂和溶剂都是常用的。在选择正确的清洁介质时,适用基于物质极性的“同类相溶”化学原理。它表明污染物在与其自身结构相似的溶剂(清洁剂)中溶解得最好(见表 1)。换言之,水基(极性)类型的污染物,例如冷却剂和润滑剂乳液、抛光膏、添加剂和盐类,通常使用水性清洁剂(亲水性)进行清洁。
为了去除非极性污染物,例如润滑油和冷却油、油脂和蜡,溶剂(亲油性)通常是首选的清洁剂。溶剂通常分为氯代烃 (CHC)、非卤代烃 (NH) 和改性醇,也称为极性溶剂 (P)。
由于改性醇具有亲脂性和亲水性,因此它们可有效去除非极性(亲脂性)和极性(亲水性)污染物。因此,它们被用作碳氢化合物以及水性清洁剂的替代品。
碳氢化合物和改性醇
健康、安全和环境问题对使用溶剂清洁工业零件的声誉产生了负面影响。但是,如果可以使用水性清洁剂或类似溶剂执行清洁任务,则使用非卤代烃或改性醇(以下也称为溶剂或烃)具有显着优势:
脱脂质量好。
通过蒸馏回收溶剂。碳氢化合物和改性醇都是可蒸馏的,这意味着进入机器并与溶剂混合的油和乳液会被连续自动去除,即使油输入量很高。此过程可确保始终如一的良好溶剂质量,从而确保始终如一的清洁质量。此外,连续再调节允许较长的溶剂寿命和低消耗。
无需质量控制。与需要定期检查 pH 值、洗涤剂浓度、电导率等的水性清洁相比,溶剂清洁不需要持续的质量控制。一个例外是在冲压和深拉等过程中使用的氯化油被带入机器时。在这种情况下,溶剂分配器会提供足够的测试设备和可能需要的稳定剂。
与几乎所有材料兼容。与水性洗涤剂不同,溶剂不会导致氧化、变色、燃烧、变暗或其他表面损伤。因此,蚀刻等化学表面效应是不可能的,但是,这些并不是实际的清洁工作。
100% 干燥部件。 即使在盲孔和隐藏通道中,溶剂也可以完全干燥零件,而无需使用热空气。
低能耗和运行成本。在溶剂清洗过程中,加热清洗液和干燥部件都需要较少的能量。此外,浴槽不需要定期控制和更换。清洁剂、淡水和废水等消耗品的成本以及废物处理成本通常也较低。
短期和长期腐蚀保护。现代溶剂清洗机允许在一个系统中执行清洗和腐蚀保护步骤。
真空技术
已经提到的对工业零件清洁中溶剂的担忧对于有时仍在使用的开顶蒸汽脱脂系统来说当然是合理的。即使是配备盖板和冷却盘管作为减排冷凝器的所谓“封闭”系统,也不是 HSE 的理想解决方案。此外,与现代、全封闭和安全的真空清洁机相比,溶剂消耗量要高得多。
这些系统配备了一个工作室和自动进料系统,一个或多个用于清洁和腐蚀保护的罐,以及一个集成的真空蒸馏系统。它们在全真空下运行——清洁、脱脂、干燥和腐蚀保护(如果适用)在一个系统中的减压气氛中进行。这种设计带来了几个好处。
没有热空气或废物
这些系统的一个好处是能够在没有能源密集型的热空气的情况下 100% 干燥零件。真空的使用使烃能够在低温下从液体完全溶解到气相中。此外,它降低了饱和蒸气压,从而增强了溶剂的毛细管传输。因此,即使是最小的盲孔和通道也很容易干燥。
通过连续真空蒸馏和溶剂处理实现低碳氢化合物消耗。分离出的油会自动从系统中排出,并在一定时间间隔后收集在废油桶中进行处理。再生的溶剂被引导回罐中以进行连续的清洁循环。这种设计允许在闭环中使用碳氢化合物,而无需进行复杂且耗时的溶剂测试,也无需处理使用过的清洁介质。不需要淡水、废水处理和化学物质分离。
操作员和环境安全
全封闭真空零件清洗机在使用碳氢化合物时无需额外的防爆保护。由于真空,机器中空气和溶剂的气态混合物的浓度被转移到不可燃区域。此外,集成冷却系统用于从废气中提取溶剂。
此外,机器操作员不与溶剂接触。待清洗的零件自动送入工作腔。直到腔室关闭并密封后,溶剂才会进入腔室。当需要添加碳氢化合物时,该过程也会自动进行,无需操作员干预。
钝化与防锈
如今,由钢和铸铁制成的零件在到达使用地点之前通过公路、空中或海上行驶数千英里的情况并不少见。因此,必须有效地保护它们免受腐蚀。如果可腐蚀的部件在使用前一直被储存起来,情况也是如此。一种相当常见的方法是将部件放入一个盒子中,有时衬有箔纸,然后将油倒在它们上面。虽然它简单快捷,但油只能到达外表面区域,而内部区域,尤其是具有复杂几何形状的零件,不受保护并开始腐蚀。
这里有一些替代方案。零件钝化:
-
临时或“短期”腐蚀保护通常在使用含有胺的水性清洁剂(中性)的水基清洁系统中进行。使用这种方法,可以实现几小时到几天的保护时间。
-
使用单独的钝化浴,保护时间可延长至数周,具体取决于胺浓度。
-
在水基系统中使用乳化油可以将保护时间延长至数月。但是,这种方法存在乳化油无法在零件表面干燥的风险,从而导致交叉污染。如果这些油在热空气干燥器中干燥,它们可能会被带走,从而导致火灾危险。此外,由于保护膜是由两相系统(水和油)形成的,因此零件表面的层通常不均匀,可能会出现斑点。
零件防锈:
-
对于“长期”腐蚀保护(保护时间从数周、数月到数年,取决于介质浓度),可使用防锈介质,例如油、油脂和蜡。由于这些介质 100% 可溶于碳氢化合物和改性醇,因此它们可用于全封闭真空清洁系统。
为执行防锈而设置的溶剂系统通常配备一个单独的罐(例如第二个或第三个食品罐),专门用于此目的。防锈罐包含碳氢化合物或改性酒精以及所需量的防锈介质。零件清洗干净后,工作腔从防锈罐中充满介质,然后进行防腐蚀过程。与清洁过程一样,它可以保证介质到达零件的所有区域。此过程之后是真空干燥过程,其中溶剂被输送回防锈罐,而防锈膜保留在零件表面。
保护膜由完全可溶、无盐的单相体系生成,零件表面的涂层均匀、完全封闭且干燥。如果触摸表面或与包装材料接触,则不会损坏。
防锈介质的选择取决于机器技术和使用的溶剂。薄膜厚度(通常在 2 到 5 微米之间)受溶剂中防锈介质浓度和滴落时间的影响。防锈介质的计量可以手动或自动完成。
保护时间、浓度
防锈介质的供应商通常会提供有关保护时间和所需浓度的信息。根据防腐产品的不同,典型的浓度介于 0.5% 和 25% 之间。它们基于实验室的经验测试,用于在检测特定校准曲线后确定薄膜重量和密度(溶剂中的百分比)。
为确定薄膜重量,按推荐浓度在标准金属板(如 Q-Panel R35)上涂抹防锈油。在此过程之前和之后对金属板进行称重。
薄膜重量是确定具有特定零件几何形状的防锈介质的大致消耗量的一种度量。另一个是膜厚。
薄膜重量 [g/m²] = 质量(防锈油)[g] / 面积(测试钣金)[m²]
膜厚 [µm] = 膜重 [g/m²] × 100 / 密度(防锈油)[g/cm³]
薄膜厚度正成为越来越重要的衡量单位,因为越来越多的零件制造商客户不仅需要介质作为腐蚀保护,还需要作为装配油。因此,必须以规定的厚度施加保护层。
由于还应在零件制造商处检查浓度,因此已开发出各种方法。使用特定的水分分析仪通过蒸发残留物进行测量是最常用的方法。它需要大约 2 克(0.07 盎司)的溶剂腐蚀保护油混合物样品。在分析仪内部,溶剂会蒸发,而剩余的油则以重量百分比的形式进行测量。然后可以用转换表确定浓度。
另一种测定浓度的方法是折射率。将一滴介质放入手动手持式折光仪。然后用户通过放大目镜观察折射率。由于折射率与温度有关,因此使用带有集成温度计的折射计很重要。可以使用 68°F、77°F 和 86°F 的介质进行测量。自动化和高度灵敏的操作测量仪器也用于密度测量。
现代的全封闭清洁系统是在单个系统中对零件进行清洁甚至长期防锈的一种有效且安全的方式。对于全球 1-3 级精密零件制造商而言,这项技术已经非常成熟。